Unleashing Potential: The Benefits of Process Simulation for Debottlenecking Natural Gas Facilities
Of course, maximizing production capacity and efficiency in the natural gas industry is paramount, and one practical approach to achieving this is utilizing process simulation to help address debottlenecking issues. In this article, we will explore how process simulation can help natural gas facilities enhance their operations and outline the numerous benefits that come with it.
What is Process Simulation?
Process simulation is a sophisticated technique that involves creating a virtual model of a facility’s processes, allowing engineers to simulate various scenarios and predict the outcomes of different operational strategies. By leveraging process simulation, these facilities can analyze every aspect of their operations, from equipment performance to process flows, without disrupting operations.
Consider a natural gas facility struggling with frequent production slowdowns, and the management team aims to increase production capacity by 20% to meet rising market demand. However, despite various adjustments, they still encounter inefficiencies and unexpected downtime.
For this situation, the facility would then turn to process simulation for a solution, with engineers beginning by gathering detailed data on the facility’s current processes, including equipment specifications and historical performance metrics. From there, they create a virtual model of the facility’s operations using advanced simulation software, accurately reflecting the real-world setup.
Through this simulation, the engineers then analyze different scenarios to identify bottlenecks, such as a specific heat exchanger causing delays due to insufficient capacity by the virtual model that allows them to test potential solutions, such as upgrading the heat exchanger or adjusting operational parameters, without disrupting actual operations.
Based on these results, the facility then implements the most effective solutions involving upgrading the heat exchanger and optimizing process flows, resulting in a 25% increase in production capacity, surpassing their initial goal.
This hypothetical example illustrates how process simulation can address common pain points like production inefficiencies by providing a clear, data-driven path to improvement by identifying and resolving bottlenecks in a virtual environment to enhance performance and capacity significantly.
Examples demonstrating the substantial improvements in production capacity that can be achieved through process simulation by identifying and addressing bottlenecks:
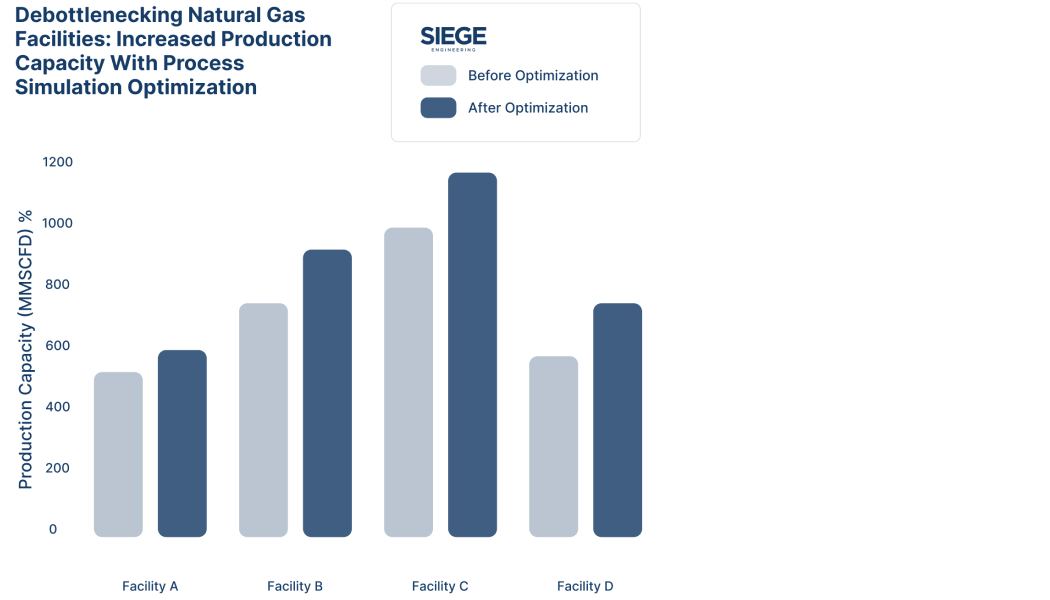
Comprehensive Benefits of Process Simulation
The advantages of these debottlenecking procedures via process simulation extend far beyond increased production capacity, as shown in the following key benefits:
- Reduced Energy Consumption and Operating Costs: By optimizing process flow and equipment usage, facilities can significantly lower their energy consumption, leading to substantial cost savings.
- Improved Product Quality and Consistency: Optimized processes result in more consistent and higher-quality outputs, ensuring compliance with regulatory standards and meeting customer expectations more reliably.
- Enhanced Safety and Reliability: Identifying potential failure points and inefficiencies through simulation helps enhance the safety and reliability of the facility’s operations.
- Minimized Environmental Impact: Efficient processes lead to reduced emissions and waste, contributing to a smaller environmental footprint.
Industry Relevance
As the natural gas industry continues to evolve, with technological advancements and stricter regulatory requirements, recent emphasis on sustainability and efficiency has made process simulation even more relevant. For example, according to a report by the International Energy Agency (IEA), optimizing natural gas processes is vital to meeting future energy demands while maintaining environmental standards.
Furthermore, the American Institute of Chemical Engineers (AIChE) highlights the growing digital transformation trend in the chemical industry, where simulation and modeling play a crucial role in operational excellence and competitiveness.
Implementing Process Simulation
For optimal results, implementing process simulation in a natural gas facility involves several crucial steps:
- Data Collection and Analysis: Gather detailed data on the facility’s processes, equipment, and operational history.
- Simulation Modeling: Utilize state-of-the-art simulation software to create a virtual model of the facility.
- Scenario Testing: Run various scenarios to identify bottlenecks and test potential solutions.
- Optimization: Implement the best solutions identified through simulation to optimize processes and enhance production capacity.
Conclusion
As discussed in the examples we have provided, process simulation is indeed a powerful tool that provides a virtual environment to test and implement solutions to maximize production capacity, reduce costs, improve quality, and enhance safety and environmental performance by adopting crucial advanced techniques like process simulation and by doing so allowing companies to maintain competitiveness and achieve operational excellence.