Scale Up Efficiently with On-Demand Process Engineering
Complex challenges when expanding a natural gas or chemical plant require meticulous planning and can easily result in unplanned downtime, budget issues, operational inefficiencies, and regulatory trouble when managed incorrectly.
In this article, we discuss impending project failure from keen observations of relevant industry data to help avoid failure with proper attention, planning, and professional execution.
The Cost of Mismanaged Plant Expansion
The consequences of inadequate management invoke many issues that can indeed result in severe consequences, such as:
Unplanned Downtime Draining Your Budget
Every minute counts when a facility goes offline unexpectedly, and in the chemical industry, this can cost an average of $100,000 per hour in lost production. For other heavy industries, the median loss can be even higher at $125,000 per hour, meaning just one day of unplanned downtime can cost an operation millions, pushing project timelines further back and adding unnecessary stress.
Surprisingly Common Budget Overruns
While expansion budgets are already exceeded far too frequently, recent studies show almost 85% of capital projects exceed their expected budgets, with the expected excesses running more in the 30–45% range above original expectations. For chemical and energy plants expanding in complexity, this recent U.S. average is even higher, at 50%, signifying that projects are running behind revenue projections, translating into millions (or tens of millions) in lost revenue, putting profit margins at risk.
Operational Inefficiencies Resulting from Poor Planning
Proper equipment layout and positioning are critical for long-term efficiency, as studies show that effective layout can reduce material handling and operational costs by approximately 10–30%. Conversely, overcrowded or poorly planned placement will frequently result in bottlenecks, complicated maintenance, and, of course, elevated safety risks.
Additional research shows errors in design contribute to approximately 79% of chemical process accidents surrounding issues such as poor equipment layouts, inadequate safety protections, and incorrect process conditions. Specifically, poor plant layout alone accounts for about 17% of these incidents, underscoring how even minor oversight in this area during expansion can significantly increase inefficiencies and safety risks.
Regulatory & Compliance Nightmares
With remedial expansions creating increased regulatory scrutiny and penalties, if an expansion or operation cannot be measured or sustained, facilities can be shut down as a result. In one prominent example, a 2019 chemical plant explosion due to safety lapses led to $1.3 million in OSHA fines, requiring immediate corrective action.
Furthermore, according to a report by the American Chemistry Council, 86% of chemical manufacturers in the U.S. experience mounting regulatory pressure, making any expansion even more complicated.
Real Pain Points for Engineers & Plant Managers
Examples of the downfall that can occur from poor management can be seen in the following aspects, all resulting in both short-term and long-term impacts on the bottom line.
- Unplanned Downtime: Imagine a newly installed heat exchanger failing just weeks after expansion due to incorrect sizing during planning, causing operations to grind to a halt and resulting in a loss of millions in production and emergency repair costs.
- Inefficient Layouts: A reactor placed in a tight, inaccessible space makes routine maintenance a multi-day ordeal instead of a simple task, leading to less productivity, higher costs, and, of course, elevated safety risks for workers.
- Compliance Issues: Installation of emissions control equipment done in a rush that results in failed updated regulatory standards, steep fines, mandatory shutdowns, costly retrofits, and severe reputational damage.
All of these scenarios demonstrate why expert guidance is crucial for navigating expansions correctly, especially for long-term potential.
Our Solution: On-Demand Senior Process Engineering
At Siege, we present a unique approach with a flexible model consisting of senior-level process engineers who are available on-demand to seamlessly integrate into your in-house team for more accurate results in planning, equipment selection, and process integration.
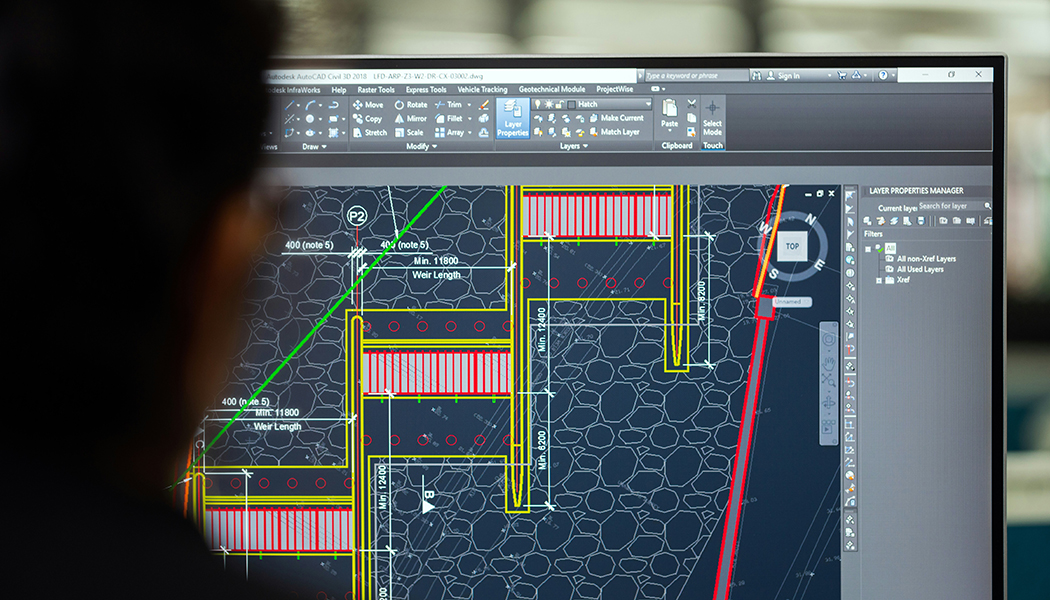
Benefits of Engaging Siege Early in Your Expansion Project
Engaging our Senior Engineers early in your project allows us to provide a full range of essential benefits that include but are not limited to:
- Cost Savings of up to 30% through expert project oversight and optimized resource allocation.
- Maximized Efficiency with precision planning and streamlined layouts that reduce long-term operational and maintenance costs.
- Proactive Compliance with every consideration associated with EPA and TCEQ regulations assessed to avoid fines and keep operations running seamlessly.
- Downtime Prevention by rigorous equipment assessment and strategic planning to drastically reduce the risk of costly downtime, keeping your expansion on schedule and on budget.
Conclusion: Your Next Steps
Are operational risks causing strain and disrupting your project? Our team of seasoned engineers is here to help you gain the knowledge, cross-functionality, and foresight necessary to prevent disasters from occurring in your operations. So reach out today for your very own complimentary consultation to begin the journey and discover how we can help you expand your existing operation with less risk and more productivity.
Contact us today to explore how we can substantially improve your bottom line!
References:
Innovapptive: Reduce Unplanned Downtime: A $20 Billion Challenge in the Chemical Industry
ABB survey reveals unplanned downtime costs $125,000 per hour
10 Construction Project Cost Overrun Statistics You Need to Hear
McKinsey & Company: Increasing transparency in megaproject execution
ICIS INSIGHT: Large construction cost overruns hit US chemical plants
Layout design for efficiency improvement and cost reduction
Design as a contributor to chemical process accidents
OSHA News Release: AB Specialty Silicones must pay $1.3M federal penalty
ACC Dramatic Rise in Regulations Undercuts American Manufacturing